Así es la adaptación de la cerámica que revolucionará la fabricación de baterías
Hay veces en que, para dar con una idea rompedora y revolucionaria, sólo hace falta mirar al pasado. Eso es lo que han hecho en Neptury Technologies, una empresa castellonense especializada en fabricación de baterías que ha desarrollado un sistema que reduce en un 35% el consumo de los materiales activos necesarios. Y lo han hecho aplicando los conocimientos que la industria cerámica castellonense desarrolló en el pasado.
La novedad ideada por esta empresa radica en un cambio sustancial en el proceso de producción de las baterías, que permite eliminar determinados procesos químicos y mecánicos de alta intensidad energética, por otros que reducen el consumo energético y material.
Charlamos con Enrique Navarro, responsable de diseño y producción de Neptury Technologies, para que nos descubra en qué consiste este método.
Un proceso sin sentido
-Primero que nada, ¿Podríais hablarnos un poco de Neptury y hacer un pequeño recorrido a través de su historia, así como vuestra especialidad?
Si bien oficialmente nos damos de alta en 2003, nacemos en 1998 con el objetivo de fabricar dispositivos de uso quirúrgico. Montamos una fábrica de marcapasos, la única que había en España. Posteriormente se vendió y montamos una fábrica en Asia diez veces más grande.
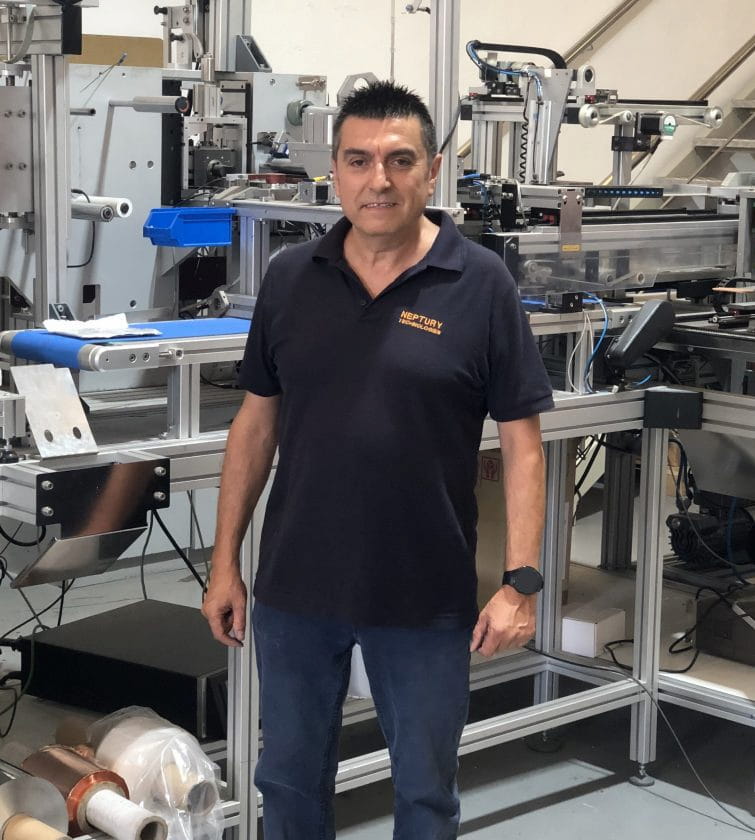
Enrique Navarro, responsable de diseño y producción de Neptury Technologies.
En 2009 exploramos otros mercados, como el de la automoción, y en 2015 un cliente nos propuso el reto de diseñar, fabricar y ejecutar una planta piloto de baterías de litio-metal, que son las que, según Tesla y Panasonic, estarán previstas para salir a la calle en 2030…
En 2020 la empresa acabó por desmantelarse porque funcionaba con capital asiático y la llevaron a Asia. En cuatro años estarán entre los cinco fabricantes más grandes del mundo.
El proceso actual de fabricación de las baterías no tiene sentido
La experiencia de todos estos años nos ha llevado a entender bastante el tema de las baterías, y, sobre todo, a hacerlo desde la base. Una vez se han ido, lo que nos ha quedado es la experiencia para poder identificar los problemas de las baterías y llegar a la conclusión de que el proceso actual de fabricación de las baterías no tiene sentido.
Igual que en los 70
-¿A qué te refieres exactamente?
Aunque parezca mentira, hoy en día las baterías se fabrican igual que en los años 70. Lo que ocurre es, debido al exponencial crecimiento de la demanda de estas baterías para la electrónica de consumo, hay tantísima demanda que todo lo que sea fabricado lo tienen vendido.
Las principales fábricas asiáticas utilizan el mismo método de producción basado en el método Roll to Roll. Nosotros no somos magos, pero tenemos la ventaja de que nos encontramos en una zona geográfica en la que ha existido una industria que tuvo un problema similar y lo solucionó.
Antiguamente la cerámica se trabajaba también roll to roll para decora mediante rodillos y se llamaba Rotocolor. Esa tecnología dio paso a la inyección digital. Nosotros hemos detectado lo que ha funcionado en otros mercados de altísima producción, como es el de la cerámica, y lo hemos trasladado al sector de la batería.
Son prisioneros de la demanda del mercado que no les permite innovar
No se puede fabricar de la forma en que se hace actualmente. Hay un derroche de materias primas exagerado. No digo que sean malvados o delincuentes industriales, sino que son prisioneros de la demanda del mercado que no les permite innovar.
Un nuevo proceso
-¿En qué consiste, por tanto, vuestro sistema?
Es una innovación en el sistema que nos permite aplicar las materias primas de una forma controlada y sostenible. Esto será un antes y un después, no porque nosotros seamos muy listos, sino porque a partir de dar a conocer este sistema que hemos creado, debemos obligar a todos los fabricantes a trabajar de esos sistemas.
No se puede tirar un 30% de materia prima a la basura, como ahora ocurre; ni podemos permitirnos el coste de energía que supone, tanto en disolventes como en la energía para secarlos.
Con nuestro sistema, además, la batería se calienta bastante menos. Hemos diseñado también unos sistemas de refrigeración de baterías internas, pensada para el automóvil. A diferencia de las baterías tradicionales, nosotros atacamos directamente la fuente interna del estrés térmico y no su consecuencia.
-¿Y en qué se puede traducir ese sistema que habéis creado?
En la carga ultrarrápida. El problema de la carga ultrarrápida es que supone una entrada de kilovatios excesiva que provoca que se caliente excesivamente. Este es el principal problema de las baterías. Ahí es donde entra nuestro sistema de refrigeración.
Con nuestro sistema podemos incluso refrigerar la batería cuando cargo. Eso se nota, sobre todo, en el uso del coche. Nosotros tenemos un demostrador forzado con resistencias a una batería, sometido a 110 grados constantes, y hemos conseguido bajarles la temperatura a 58 grados. Además, al ser interna, podemos bajar hasta 10 grados en la parada de un minuto en el semáforo.
Mirar dentro de casa
¿Qué influencia puede tener vuestro descubrimiento en la Comunidad Valenciana, que busca ser un hub del coche eléctrico?
Yo no quiero vender que podemos hacer tal o cual cosa. Creo que debemos hacerlo simplemente por sentido común. Como en el caso de la cerámica, desde hace más de una década ya nadie se plantea trabajar con Rotocolor; de la misma forma debería ocurrir con las baterías.
No tendría ningún sentido que la Comunidad Valenciana tratase de atraer una fábrica asiática para hacer las baterías con el sistema y la dinámica tradicional. No cuando tenemos aquí un sistema desarrollado por nosotros que los asiáticos acabarán por adoptar mañana.
En el panorama internacional ya existen planes de trabajar con esta tecnología en 2025. Han hecho unas inversiones multimillonarias y eso demuestra que el futuro va por aquí.
Nuestro proceso tiene otras ventajas. Por ejemplo, los estratos los secamos por inducción, con una tercera parte de la energía que los sistemas tradicionales. Por inducción, con muy poca temperatura y con gran eficiencia, conseguimos secarlo con mucho menos gasto energético.
Si en la Comunidad Valenciana quiere avanzar en este sentido, debe adoptar tecnologías sostenibles, no seguir con métodos tradicionales que se van a acabar.
Nuevos desarrollos
¿Tenéis pensado algún nuevo proyecto futuro?
Estamos trabajando ahora mismo con el hidrógeno, en un proyecto muy serio con hidrolizadores para el futuro. En España es el proyecto más serio que yo haya visto. Lo más impresionante es que para desarrollarlo iban a comprar los sistemas tradicionales y cuando vieron nuestra tecnología cambiaron de opinión.
Lo importante es que los fabricantes tomen nota, porque son los ganadores de la Champions Leage del derroche de materia prima
Estamos fabricando también una máquina inject como parte de nuestro motor de prueba, para ver qué pasa. Ya hay multinacionales que lo han visto. Lo importante es que los fabricantes tomen nota, porque son los ganadores de la Champions Leage del derroche de materia prima.