Incentivación por productividad
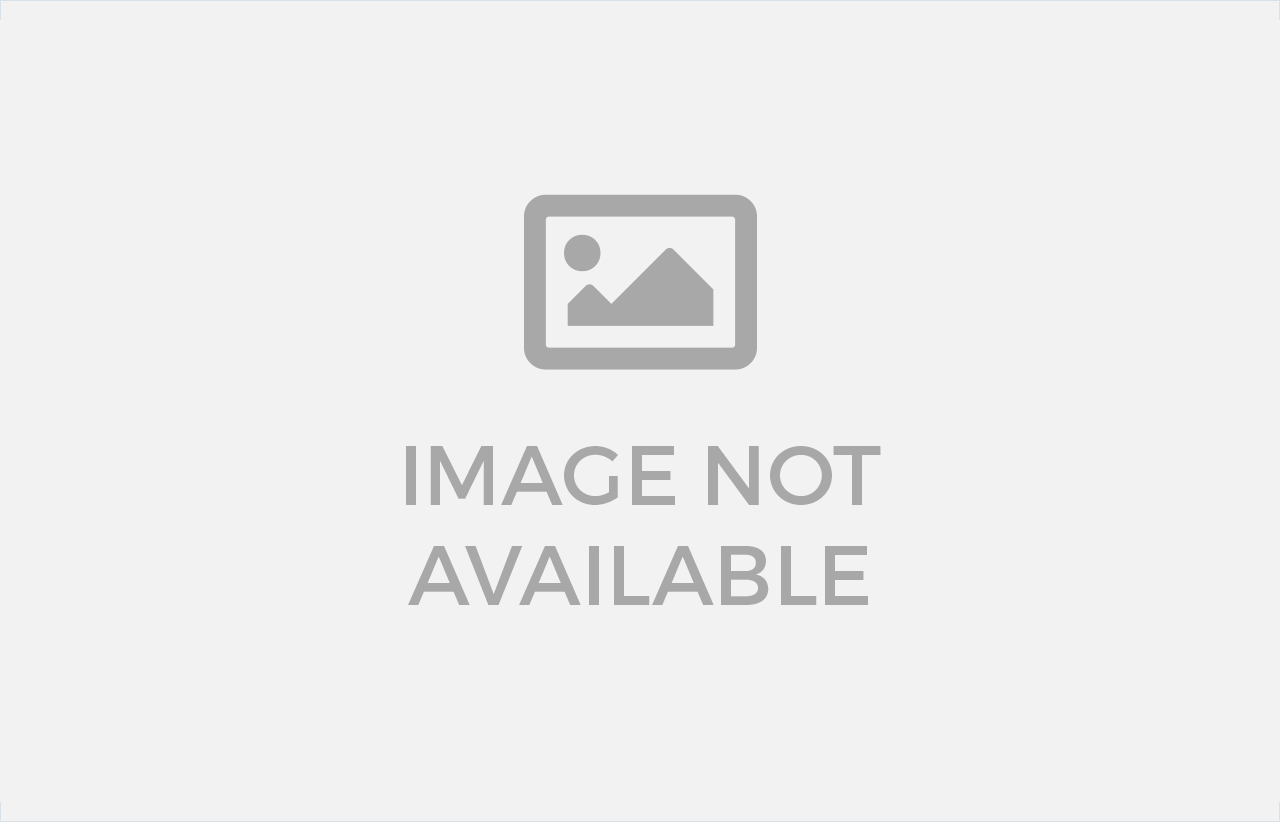
Socio Fundador. Consultores de Productividad y Logística
Durante los últimos meses, muchas empresas han solicitado los servicios de nuestra consultora para implementar (o actualizar) los sistemas de incentivos a partir de la medición de la productividad de la mano de obra (tanto directa como indirecta). Y no ha sido un caso aislado. Lo han requerido tanto pymes como multinacionales. Y en sectores variados como el del plástico, la logística, la metalurgia, cartonajes, alimentación, etc.
Nuestra propuesta ha sido constante: se trata de una herramienta encaminada a mejorar los beneficios empresariales. Lo primero que deberemos definir son los estándares de trabajo. En segundo lugar, correspondería homologarlos ante los operarios (homologación entendida como práctica generalmente aceptada y cumplida), en tercer lugar se procederá a la medida del trabajo, determinando el tiempo requerido para desarrollarlo según el estándar definido de prestación por parte de un operario cualificado para, opcionalmente, fijar con posterioridad el Sistema de Retribución Variable en función de la Eficiencia Total, estandarizando la Velocidad de las Máquinas, el Cumplimiento del Método, tanto en Producción como en los Cambios, la Minimización de las Mermas y Retrabajos y la Disminución de los Tiempos de Averías, Espera y Paros.
Pero insistamos en el primer paso a dar: ¿Qué es un Estándar de Trabajo?
Un Estándar de Trabajo es una descripción escrita sobre cómo debe realizarse un proceso. El estándar sirve para disponer una ejecución consistente, creando una voluntad de conseguir “mejores prácticas”. Como mínimo, el estándar proporciona una línea de base a partir del cual se puede desarrollar un mejor (y más barato) enfoque.
Una vez definido el método, es necesario concretar los tiempos para su realización. De esta manera, todo el mundo participa en ver cómo el estándar está funcionando y todo el mundo tiene la oportunidad de descubrir nuevas oportunidades para mejorar aún más. Los indicadores básicos son:
Tiempo Takt, Tiempo de ciclo, Relación de valor añadido, Throughput (unidades de producción por unidad de tiempo), Costo unitario, Tasa de defectos o conformidad, Tasa de chatarra, Tiempo de funcionamiento de la máquina (si las máquinas están involucradas), Porcentaje de tiempo de ciclo de las máquinas y Saturación de los operarios.
La medida de trabajo se debe realizar, bien mediante las técnicas tradicionales de Cronometraje, bien mediante técnicas Modapts. Los tiempos utilizados en los códigos Modapts muestran el tiempo necesario para que la parte del cuerpo en la que se desarrollará la acción la emplee a un ritmo cómodo, que podría mantenerse como parte de un ciclo de trabajo de un día completo de la jornada laboral. Modapts se utilizará especialmente para establecer un tiempo razonable y sostenible para completar el método de trabajo propuesto, sirviendo así mismo para impulsar la estandarización del mejor método y el diseño del lugar de trabajo con que llevar a cabo una tarea determinada, equilibrando el flujo de trabajo, desarrollando procedimientos operativos estándar, instrucciones de trabajo y proporcionando un marco para el análisis de las acciones y posturas en el trabajo (ergonomía).
Para implantar un Sistema de Retribución Variable en función de la Eficiencia Total, los elementos básicos que regulen el Sistema de Incentivación por Productividad serán:
1. Consecución del Coste Horario Igual o Inferior al Estándar.
2. El Trabajo Estandarizado en los momentos de Cambios en las Máquinas (o limpiezas en la industria de la alimentación) seguirán las directrices emanadas al aplicar el Sistema Smed, una metodología contrastada y habitual en la aplicación de las herramientas Lean Manufacturing y que se basa en una estricta metodología para separar las actividades internas de las externas, así como balancear lo máximo posible el trabajo de los distintos operarios.Un ejemplo de ello se muestra en los gráficos reproducidos, donde se compara el método tradicional de un cambio en una Troqueladora Rotativa del cartón y el método Smed. El Estándar de Trabajo no consiste en aumentar la velocidad del operario sino en disminuir las tareas que no aportan valor (en este caso los movimientos).
3. Consecución de la Calidad Requerida por el Cliente, con exigencias de un número máximo de rechazos por millón.
4. Reducción de Desperdicios (materias primas y/o productos semielaborados) que no superen un tanto por mil como Estándar del Coste Final del producto.
5. Consecución, mediante las herramientas pertinentes dentro del Sistema TPM (Total Productive Mantenaince) como una metodología contrastada y habitual en la aplicación de las herramientas Lean Manufacturing de un Rendimiento Estándar (Tiempo Efectivo de Trabajo sobre Tiempo Completo).
6. Puntualidad en el servicio (entregas completas y a tiempo), puesto que la Planificación “Justo a Tiempo” es la herramienta común de nuestros clientes en particular y el Mercado al que se dirigen nuestras ventas en general.
7. Cero Devoluciones y/o Reclamaciones.
8. Reducción a niveles Estándar de los Retrabajos.
9. Al objeto de perseguir un clima de Mejora Continua, la totalidad de la Mano de Obra (tanto Directa como Indirecta o el de las Funciones Soporte) deberán tener una gran implicación en su contribución positiva en las Reuniones de los Equipos de Mejora de la Productividad a Pie de Máquina.