Jornada industria 4.0 ( y III) La digitalización está al alcance de cualquier empresa, de cualquier sector
La mesa de expertos de la Jornada Industria 4.0 sirvió para conocer la experiencia de la puesta en marcha de proyectos de digitalización en tres industrias muy diferentes, tanto por producto como por dimensiones y facturación, de modo que se pudo comprobar que la digitalización está al alcance de cualquier empresa.
Participaron en la tertulia Sebastián Cano, gerente de IML Robotics Solutions; Gabriel García, Director General de THU Ceiling Solutions, y Eduardo Martín, Director de Logística de ArcelorMittal en Sagunto.
De la robótica a la siderurgia
Sebastián CanoIML es una empresa de robótica con sede en Ibi y cuenta también con una filiar el Carolina del Norte. Cano señaló que en un sector tan competitivo como el suyo es preciso diferenciarse y, sobre todo, dar muy buen servicio. Por ello han adoptado industria 4.0 para la mejora de sus productos y servicios a los clientes. El avance que han incorporado es la recopilación de datos y su tratamiento para realizar un mantenimiento predictivo de sus robots, de forma que avisan al cliente de que en determinado plazo pueden sufrir una parada por desgaste de alguna pieza, tiempo que servirá para reemplazarla, de forma que no se produzca ninguna pérdida.
Además, IML ha incorporado la información colaborativa con las máquinas, de forma que el cliente con gafas de realidad aumentada puede compartir información. «De esta forma -aseguró Cano– nuestros técnicos pueden seguir en tiempo real cualquier máquina nuestra en cualquier parte del mundo y asesorar como cambiar un componente».
Gabriel GarcíaGabriel García, de THU Ceiling Solutions, una pyme con una facturación de 15 millones de euros que fabrica perfilería para la construcción (pladur y falsos techos). Han sorteado la crisis gracias a la internacionalización y la implementación de nuevos procesos que les han hecho más eficientes, algo absolutamente necesario en un sector tan competitivo como el suyo. El primer paso fue instalar sensores que automatizó la recopilación de información de producción que con anterioridad se recopilaba a mano. García puso énfasis en la necesidad de explicar muy bien la implementación de estos sistemas a la organización para que haya éxito.
Eduardo Martín también admitió que en ArcelorMittal se ha llegado a la industria 4.0 por la necesidad de ser más productivos. Con más de 200.000 metros cuadrados de superficie, la planta dispone de un tren interior para mover las bobinas desde la factoría hasta el puerto o la playa de vías. Con la simple colocación de una cámara en la locomotora se consigue desde captar datos del estado de la vía y adelantarse a averías que puedan surgir y parar el proceso productivo. Este mismo sistema instalado en los puentes-grúa que permitirá detectar roturas en los carriles.
Otra de las implementaciones es el control de operaciones de la locomotora, de forma que muchas de ellas se podrán realizar telemáticamente, con lo que la locomotora solo precisará de una persona para atenderla.
Contacto permanente con el cliente
Cano afirmó que aunque ahora es raro ver por la factoría a alguien con gafas de realidad aumentada, en el futuro cercano será algo habitual, comunicándose con las máquinas. «El futuro de la industria -aseguró- es, por supuesto, todo digitalizado. Por ejemplo, cuando abras un armario eléctrico verás en las gafas de realidad aumentada todos los esquemas, seleccionar componentes e incluso puedes acceder a los manuales para realizar los ajustes necesarios. Por ejemplo, nuestros clientes pueden solicitarnos un recambio seleccionándolo a través de la realidad aumentada, lo que mejora la interconectividad y evita errores».
Eduardo MartínPara Gabriel García las restricciones a la digitalización es la inversión que supone. «Nuestra estrategia es clara. A corto plazo, cuando terminemos la digitalización de los procesos, seguiremos con el almacén», aseguró.
En el caso de ArcelorMittal, el reto ha sido formar a los transportistas en el uso de la plataforma que contrata el transporte de las bobinas. Lo que, admitió Martín, al principio les parecía complicado, gracias a una app, el proceso ha ido perfectamente. «Los proveedores y los clientes te exigen que las cosas funcionen de esa manera, porque es mucho más fácil. Cualquiera sabe manejar un móvil. Esto es un factor disruptivo que va a aumentar la productividad de todo el mundo».
¿Cómo va a ayudar industria 4.0 a mejorar la relación con nuestros clientes? A esta pregunta los participantes en la mesa coincidieron en que era decisiva. En el caso de IML, «supone mantener contacto con una máquina que a lo mejor está en la otra punta del mundo. Pretendemos que el cliente pueda entrar en contacto con nosotros en cualquier momento para lo que necesite, desde una teleasistencia a una pieza de recambio. Es muy importante crear esa relación».
Recursos humanos
Gabriel García, por su parte, agregó que su prioridad es la productividad, poder ofrecer el mejor precio, siendo eficientes en costes. Mientras, ArcelorMittal ha observado que las necesidades se están centrando en el transporte más que en la producción: «El cliente quiere saber en qué vagón está determinada bobina».
Este salto tecnológico, ¿cómo va a afectar al factor humano? Dependiendo del sector, puede no tener ningún impacto o, por el contrario, hacer superfluos algunos puestos de trabajo. IML asegura que en su caso no se ha prescindido de trabajadores, «pero sí han tenido que formarse para manejar los robots. Normalmente, nuestros clientes aumentan de tamaño y de personal». García admitió que si no se explica bien pueden existir recelos, pero aumentar la productividad es una salvaguarda del empleo. «Permite medir de forma objetiva la productividad de cada empleado. Ahora están muy satisfechos porque saben que es bueno para la empresa y del trabajo que hacen». Martín admite que, en el caso de ArcelorMittal, sí han reducido bastantes empleos.
Artículos relacionados
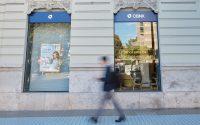
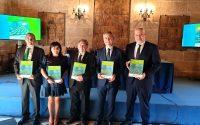